检测对象无纺布
检测精度0.1mm
检测幅宽任意宽度
缺陷类型蚊虫,异物,杂质,脏污,孔洞大小分布不均等
测宽精度<0.2mm
缺陷标识自动声光报警,自动贴标
检测速度Max 600m/min
历史记录检测过程全记录
响应时间24小时实时在线
控制方式自动
本检测系统采用的图像识别技术,能精准检测无纺布表面的各类缺陷,如孔洞、污渍、断丝等。快速反馈结果,助力提升产品质量,降低次品率,适用于各类无纺布生产企业。
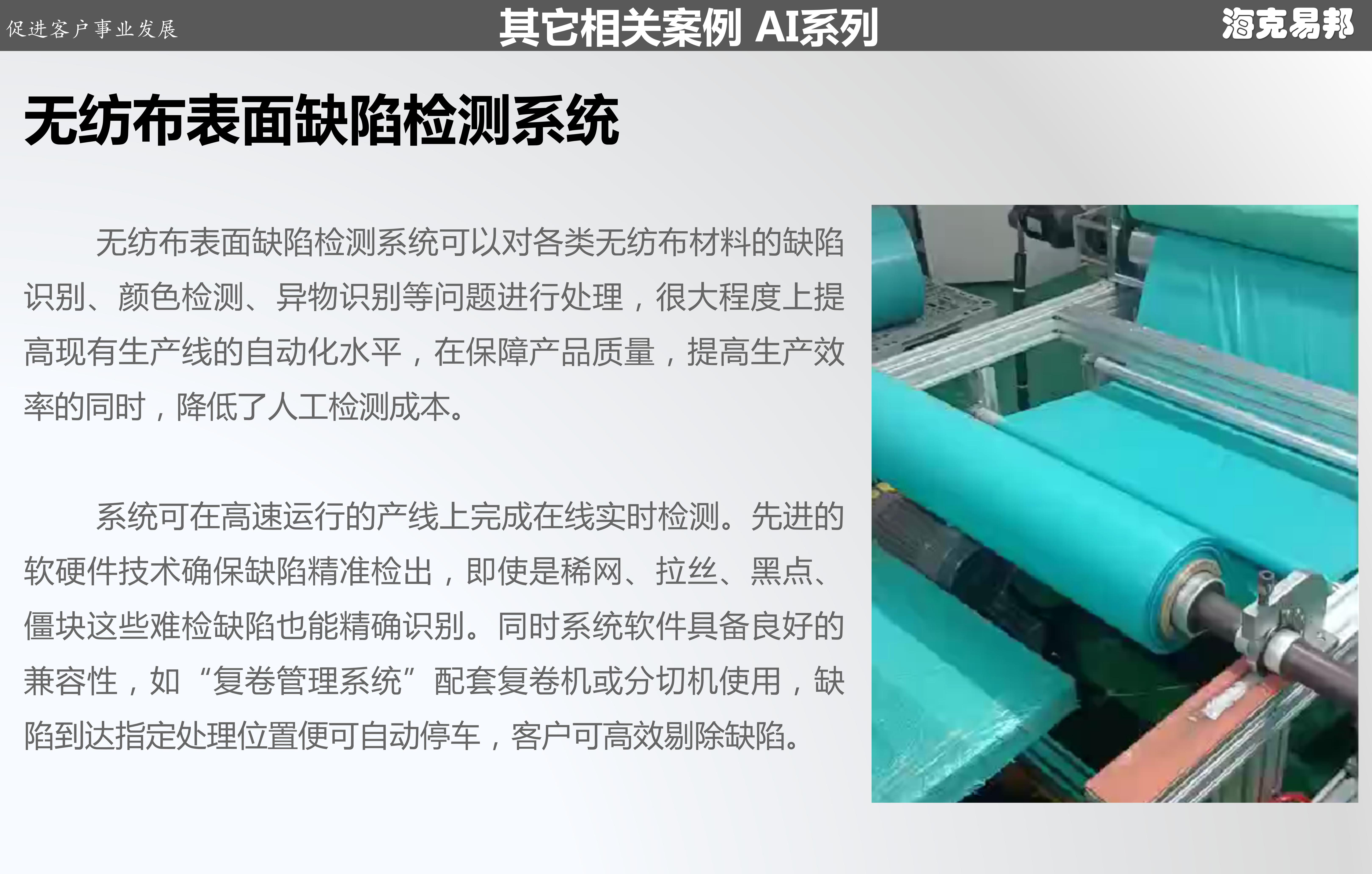
一、系统组成部分
图像采集模块
摄像头:
采用高分辨率的工业摄像头,以确保能够清晰地捕捉无纺布表面的细节。摄像头的分辨率、帧率等参数需要根据无纺布的生产速度和检测精度要求进行选择。例如,对于高速生产的无纺布生产线,可能需要帧率较高(如 100 - 200 帧 / 秒)的摄像头来避免图像模糊。
照明系统:
合适的照明对于获取量图像至关重要。通常采用均匀的背光源或侧光源,以**无纺布表面的缺陷特征。例如,对于检测无纺布上的孔洞等缺陷,背光源可以使孔洞在图像中显示为较暗的区域,便于识别。
图像处理与分析模块
计算机视觉算法:
基于机器学习或传统图像处理算法。在机器学习方面,卷积网络(CNN)被广泛应用。例如,通过大量带有标记的无纺布缺陷图像(如划痕、污渍、孔洞等不同类型缺陷的图像)对 CNN 模型进行训练,使其能够自动识别新图像中的缺陷类型和位置。
传统图像处理算法包括阈值分割、边缘检测等。阈值分割可以将图像分为目标区域(可能的缺陷区域)和背景区域,例如,设定合适的灰度阈值,将灰度值低于或**该阈值的像素判定为缺陷像素。边缘检测算法如 Canny 边缘检测,可以检测出缺陷的边缘轮廓,从而确定缺陷的形状和大小。
软件平台:
用于运行图像处理算法和管理检测系统的操作界面。它可以实现参数设置(如算法阈值、检测区域等)、检测结果显示(包括缺陷类型、位置、大小等信息)以及数据存储和管理等功能。
控制与反馈模块
控制器:
与生产设备相连接,根据检测结果对生产过程进行控制。例如,如果检测到无纺布表面存在严重缺陷,控制器可以发出信号,使生产设备停止运行,避免生产出更多的次品。
反馈机制:
将检测结果反馈给生产管理系统,以便对生产工艺进行调整。例如,如果发现某一时间段内某种缺陷出现的频率较高,生产管理系统可以调整原材料配比、生产速度或设备参数等。
二、检测的缺陷类型
孔洞缺陷
成因:
可能是由于原材料中的杂质、生产过程中的机械损伤(如针刺不当)等原因造成。
检测方法:
通过图像中的灰度变化来检测。孔洞区域在图像中通常表现为明显的低灰度区域,与周围正常无纺布的灰度差异较大。利用阈值分割算法可以有效地将孔洞区域从背景中分离出来。
划痕缺陷
成因:
可能是在无纺布生产过程中的摩擦、运输过程中的刮擦等引起。
检测方法:
基于边缘检测算法。划痕在图像中表现为连续的边缘,通过 Canny 等边缘检测算法可以检测出划痕的边缘轮廓,进而确定划痕的长度、宽度和位置等信息。
污渍缺陷
成因:
可能是原材料污染、生产环境中的灰尘等附着在无纺布表面。
检测方法:
可以利用颜色特征或灰度特征进行检测。如果污渍与无纺布本身颜色有明显差异,可以在彩色图像空间(如 RGB 空间)中进行颜色阈值分割。如果在灰度图像中,污渍区域的灰度值也可能与正常区域有差异,通过设定合适的灰度阈值同样可以检测到污渍。
三、系统的优势
提高产品质量
通过及时准确地检测出无纺布表面的缺陷,可以避免有缺陷的产品进入下一道工序或流向市场,从而提高终产品的质量。
提高生产效率
减少人工检测的工作量,人工检测不仅速度慢、效率低,而且容易疲劳导致漏检。自动化的检测系统可以持续高速地对无纺布进行检测,并且能够适应较高的生产速度。
数据统计与分析
系统可以对检测数据进行统计和分析,如缺陷类型的频率分布、不同时间段内缺陷出现的规律等。这些数据对于优化生产工艺、提高生产管理水平具有重要意义。
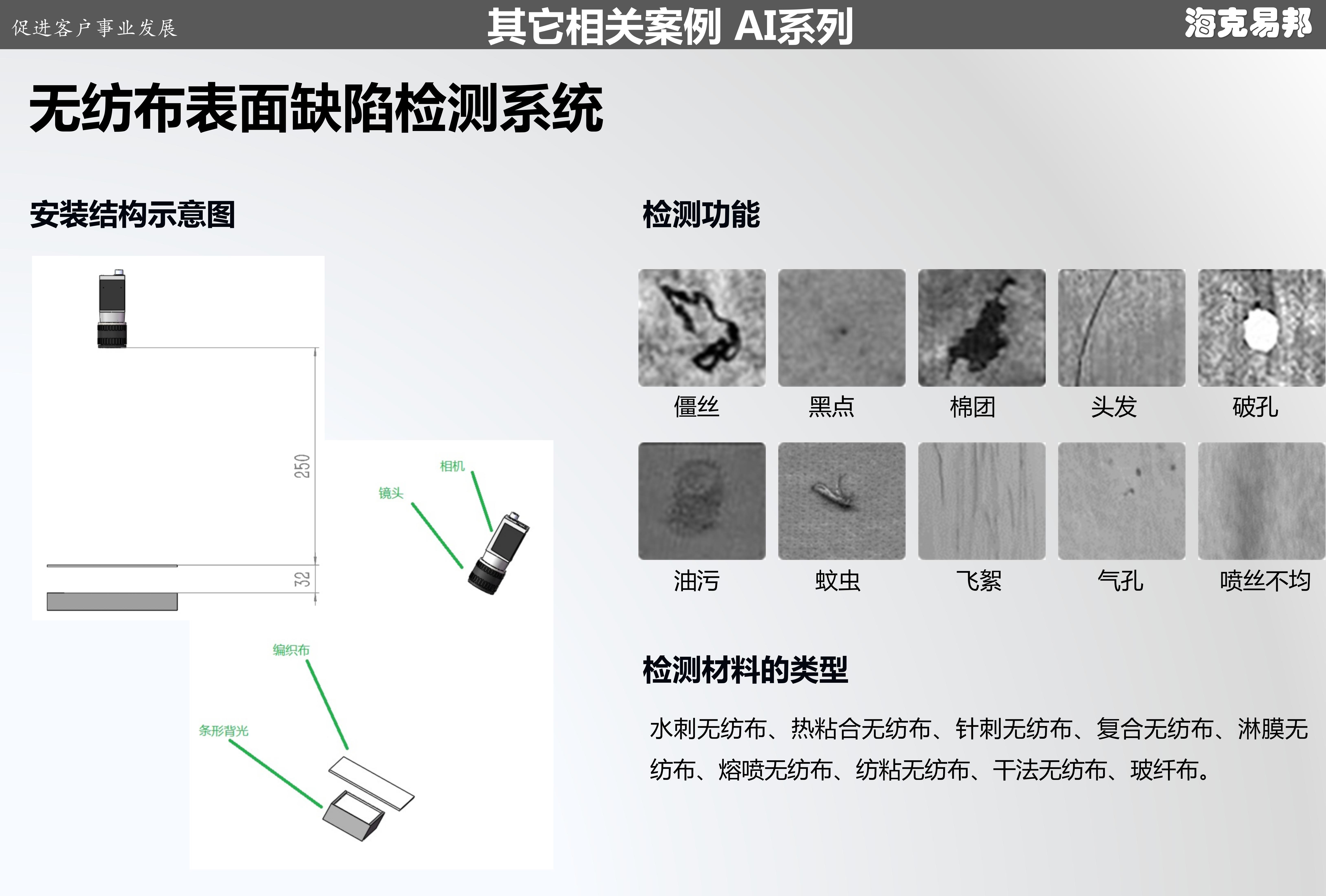
无纺布视觉检测系统是一种利用计算机视觉技术对无纺布进行检测的智能化系统,以下是详细介绍:
一、系统概述
定义与目的
定义:无纺布视觉检测系统是将光学成像设备获取的无纺布表面图像,通过计算机视觉算法进行处理和分析,以检测无纺布表面是否存在缺陷、确定缺陷类型和位置的系统。
目的:**无纺布的质量,提高生产效率,降低生产成本,同时为生产工艺的改进提供数据支持。
二、系统主要组成部分
图像采集单元
相机:
类型选择:根据检测需求可选用面阵相机或线阵相机。面阵相机适用于检测静止或慢速移动的无纺布,能够一次性获取整个检测区域的图像;线阵相机则更适合高速连续生产的无纺布生产线,通过逐行扫描获取图像。
分辨率要求:为了能够清晰地检测出微小的缺陷,相机需要具备较高的分辨率。例如,对于一些的无纺布视觉检测系统,相机分辨率可能达到百万像素甚至更高。
镜头:
焦距选择:根据检测区域的大小和工作距离确定合适的焦距。如果检测区域较大且工作距离较远,需要选择长焦镜头;反之,对于较小的检测区域和较短的工作距离,短焦镜头可能更合适。
光圈调节:光圈大小影响进光量和景深。在检测无纺布时,需要根据照明条件和对景深的要求合理调节光圈,以确保图像的清晰度和对比度。
照明系统:
照明方式:常见的有背向照明、正向照明和侧向照明。背向照明适用于检测无纺布上的孔洞等透明或半透明缺陷,因为这些缺陷在背向照明下会呈现出明显的暗区;正向照明可以均匀照亮无纺布表面,用于检测表面的污渍、划痕等缺陷;侧向照明则有助于**无纺布表面的纹理和边缘特征,可用于检测无纺布的边缘缺陷或表面不平整情况。
光源类型:可以选择 LED 光源,因为 LED 光源具有寿命长、亮度高、可调节性强等优点。
图像处理与分析单元
硬件平台:
通常采用高性能的计算机或专门的图像处理硬件设备,如 GPU(图形处理单元)加速卡。GPU 具有强大的并行计算能力,能够加速图像处理算法的运行速度,满足实时检测的需求。
软件算法:
预处理算法:包括图像滤波、灰度变换等。图像滤波可以去除图像中的噪声,例如采用高斯滤波可以平滑图像,减少噪声对后续检测的影响;灰度变换可以增强图像的对比度,使缺陷更加明显,如直方图均衡化算法。
特征提取算法:根据无纺布的特性和缺陷类型提取相关特征。对于孔洞缺陷,可以提取孔洞的面积、形状等特征;对于划痕缺陷,可以提取划痕的长度、宽度、方向等特征。这些特征可以通过形态学操作、边缘检测算法(如 Sobel 边缘检测、Canny 边缘检测)等方法来提取。
分类与识别算法:利用机器学习或深度学习算法对提取的特征进行分类和识别。在机器学习方面,可以采用支持向量机(SVM)、决策树等算法;在深度学习领域,卷积网络(CNN)是目前应用为广泛的算法,通过大量的标注样本对 CNN 模型进行训练,使其能够准确识别不同类型的无纺布缺陷。
控制与决策单元
控制器:
与生产设备进行连接,根据检测结果控制生产设备的运行状态。例如,如果检测到无纺布存在严重缺陷,控制器可以立即停止生产设备,防止更多的次品产生。
决策算法:
根据检测到的缺陷信息和预先设定的质量标准,做出相应的决策。例如,对于轻微缺陷的无纺布,可以根据其缺陷的类型和严重程度决定是否允许其进入下一道工序,或者将其标记为次品进行分类处理。
三、检测的主要内容
缺陷检测
孔洞:通过图像中的灰度差异或形状特征来检测无纺布上的孔洞。孔洞在图像中通常表现为与周围正常区域明显不同的低灰度区域或圆形、不规则形状的区域。
划痕:利用边缘检测算法检测无纺布表面的划痕。划痕在图像中显示为连续的边缘线条,通过分析边缘的长度、宽度和连续性等特征来确定划痕的严重程度。
污渍:根据颜色特征或灰度特征识别污渍。如果是彩色无纺布,可以在 RGB 或其他颜色空间中分析颜色的异常变化;对于灰度无纺布,可以通过设定灰度阈值来检测污渍区域。
厚度不均:虽然视觉检测不能直接测量无纺布的厚度,但可以通过检测无纺布表面的纹理、光影变化等间接推断出厚度是否均匀。例如,较厚的区域可能在图像中表现出较暗或较亮的区域,以及纹理的变化。
尺寸测量
宽度测量:对于无纺布卷材,可以准确测量其宽度,确保其符合生产规格要求。通过在图像中确定无纺布边缘的位置,计算出边缘之间的距离来得到宽度值。
长度测量:在生产过程中,可以对无纺布的长度进行实时测量,便于生产管理和产品包装。可以通过对生产线上无纺布的移动速度和检测时间进行积分计算出长度。
四、系统的应用优势
质量提升
高精度检测:能够检测出微小的缺陷,提高无纺布产品的整体质量。
一致性**:确保产品质量的一致性,符合严格的质量标准。

视觉检测方法
直接观察法
原理:
操作人员直接用肉眼观察无纺布喷丝的情况。这是一种基本的方法,在生产过程中,有经验的工人可以快速发现喷丝头是否存在明显的喷丝不均现象,例如某一区域的丝明显比其他区域稀疏或密集。
局限性:
主观性强,不同操作人员的判断标准可能存在差异。而且对于一些细微的喷丝不均情况,肉眼可能难以准确识别。
机器视觉检测
原理:
利用摄像头等图像采集设备获取无纺布喷丝的图像,然后通过图像处理算法进行分析。例如,将采集到的图像转换为灰度图像,计算图像的灰度值分布。均匀喷丝的无纺布在图像上的灰度值分布相对均匀,而喷丝不均的区域会出现灰度值的突变。
还可以通过边缘检测算法,检测喷丝纤维的边缘轮廓。正常喷丝情况下,纤维边缘轮廓应该是相对规则和平滑的,如果存在喷丝不均,边缘轮廓会出现不规则性,如局部的锯齿状或者不连续等。
优点:
检测精度高,可以检测到肉眼难以察觉的喷丝不均情况。并且检测速度快,能够满足大规模生产线上的实时检测需求。
关键技术及设备要求:
需要量的摄像头,其分辨率要足够高以清晰捕捉喷丝的细节。同时,配套的图像处理软件需要具备准确的算法,并且能够根据不同的无纺布生产工艺和产品要求进行参数调整。例如,对于不同纤维粗细、喷丝密度的无纺布,算法中的阈值等参数可能需要重新设定。
http://hkeb02.cn.b2b168.com